CNC LATHE/ TURNING CONTROLLER
GSK 980TD
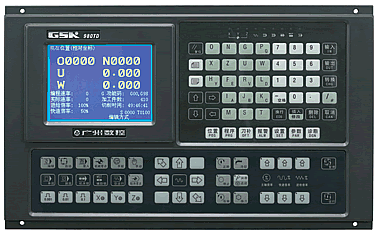
|
Introduction
With 32-bit high performance CPU and super-large-scale programmable FPGA, the new generation widespread GSK980TD Turning Machine CNC System developed by us (GSK CNC Equipment Co., Ltd.) is the upgraded product of GSK980TA, applying the real time multitasking control and hardware interpolation technology to realize ฆฬ m-level precise motion and PLC logic control |
-  Link axes (X, Z), ฆฬ m-level interpolation precision and max. rapid traverse speed 16 m /min(option: 30m /min);
- Â Embedded PLC to control various of automatic toolposts and spindle automatic shifting gear, edit, transmit and download ladder diagrams; expendable I/O interfaces(optional function)
- Â Tapping to machine metric/inch single/multiple straight, taper thread, end face thread, variable pitch thread, high speed thread run out with set retraction distance, angle and speed ;
- Â Pitch error compensation, backlash compensation, tool length compensation and tool nose radius compensation ;
- Chinese and English display interface selected by parameters ;
- S, exponential acceleration/deceleration control to meet high speed and high precision machining ;
- Large memory capacity(6144KB,384 part programs) with full screen edit ;
- Convenient management for the system with multilevel operation password ;
- Bidirectional communication between CNC and PC, CNC and CNC; communication upgrading CNC software and PLC programs ; Installing dimension, electric interfaces, instruction system and operating windows being compatible with GSK980TA Turning CNC System .
|
  Technical specification |
Motion control
 |
Controllable axes: 2(X, Z); simultaneous controllable axes: 2 (X, Z) |
Interpolation: linear, arc interpolation in X, Z direction |
Dimension for programs: -9999.999 ~ 9999.999mm ; min. unit: 0.001mm |
Electronic gear : instruction multiplying 1 ~ 32767 and dividing 1 ~ 32767 |
Rapid traverse speed: max. 16000mm /min(option: 30000mm /min)
Rapid override: time real tuning F0 , 25% , 50% , 100% |
Cutting feedrate: max .8000mm /min(option: 15000mm /min) or 500mm /rev(feedrate per rev)
Feedrate override: 16 steps real time tuning for 0 ~ 150% |
Manual feedrate: 16 steps real time tuning for 0 ~ 1260mm /min |
Handwheel feedrate: 0.001 , 0.01 , 0.1mm |
Acceleration/deceleration: S acceleration/deceleration for rapid traverse movement and exponential acceleration/deceleration for cutting feed |
G
functions |
28 kinds of G instructions: G00, G01, G02, G03, G04, G28, G32, G33, G34, G40, G41, G42, G50, G65, G70, G71, G72, G73, G74, G75, G76, G90, G92, G94, G96, G97, G98, G99 and macro instruction G65 to execute 27 kinds of calculation, logic operation and program jumping |
Thread machining
 |
Tapping to machine metric/inch single/multiple straight thread, taper thread, end face thread, variable pitch thread. High speed thread run out with set retraction distance, angel and speed; pitch: 0.001 ~ 500mm or 0.06 ~ 25400 tooth/inch |
Spindle encoder: lines can be set ( 100 ~ 5000p/r ) |
Drive ratio between encoder and spindle: ( 1 ~ 255 ):( 1 ~ 255 ) |
Precision compensation |
Backlash compensation: ( X, Z ) 0 ~ 2.000mm |
Pitch error compensation: 255 compensation points with ± 0.255mm × compensation override for each one in X, Z direction |
Tool compensation: 32 groups tool length compensation, tool nose radius compensation (tool compensation C)
Toolsetting method: fixed-point toolsetting, trial cutting toolsetting
Tool compensation executing methods: traversing tool or coordinate offset |
M
instructions |
M instructions(no repetition): M02, M30, M98, M99, M9000 ~ M9999 Other M ?? instructions are defined and executed by PLC programs |
M instructions defined by standard PLC program: M00, M03, M04, M05, M08, M09, M10, M11, M12, M13, M32, M33, M41, M42, M43, M44 |
T
instruction |
Most 32 tool selections ( T01 ??~ T32 ??) , the time sequence of tool change is defined by PLC programs. The tool selection is set to 1 and the tool change is not executed by PLC when the line-up toolpost is employed. The standard PLC programs is s is optional to 2 ~ 8 tool selections toolpost, clockwise rotation for selecting tools and counterclockwise rotation for clamping toolpost. |
Spindle speed |
Speed switching value control: S ?? instruction is defined and executed by PLC programs, direct output of S1, S2, S3, S4 is controlled by the standard PLC programs and S0 is used for stopping output of S1, S2, S3, S4 |
Speed analog voltage control: S instructions specifying the spindle speed per minute or the cutting surface speed (constant surface speed control) , the system outputting 0 ~ 10V voltage to spindle inverter, 4 gears spindle speed with stepless shifting gear |
PLC
function |
9 kinds of elementary instruction, 23 kinds of function instruction, 2 grades PLC program, max. 5000 steps an d 2 ฆฬ s for each step, refresh cycle for the first grade program is 8ms, ladder diagram editing software, PLC program communication download |
Integrated machine control panel: 41 input points (press keys), 42 output points (LED)
Basic I/O interfaces: 16 input points /16 output points (optional I/O interface: 16 input points /16 output points) |
Displaying window |
Display: 320 × 240 lattice, 5.7à¸à¸‘ monochrome liquid crystal display(LCD), CCFL in a poor light |
Display method: Chinese or English window is set by parameter, displaying machining path of workpiece |
Program editing
 |
Program capacity: 6144KB, max. 384 programs, supporting user macro program calling and four-embedded subprogram |
Editing method: incremental coordinates, absolute coordinate and compound coordinates programming with full screen edit |
Communication |
Bidirectional communication for programs and parameters between CNC and PC, CNC and CNC; communication upgrading and downloading CNC software and PLC programs |
Optional driving |
DA98 Series Digital AC Servo or DY3 Series Stepper Driver with input pulse and direction signal |
Â
Support Manual
|
Controller 980TD for turning manual |
G instructions |
Instructions |
Functions |
Instructions |
Functions |
G00 |
Positioning (Rapid traverse movement) |
G70 |
Finishing cycle |
G01 |
Linear interpolation(cutting feed) |
G71 |
Axial roughing cycle |
G02 |
Clockwise circular interpolation (rear toolpost) |
G72 |
Radial roughing cycle |
G03 |
Counterclockwise circular interpolation(rear toolpost) |
G73 |
Closed cutting cycle |
G04 |
Dwell |
G74 |
Axial grooving cycle |
G28 |
Machine reference point return |
G75 |
Radial grooving cycle |
G32 |
Thread cutting |
G76 |
Multiple thread cutting cycle |
G33 |
Tapping cycle |
G90 |
Axial cutting cycle |
G34 |
Thread cutting with variable lead |
G92 |
Thread cutting cycle |
G40 |
Canceling tool nose radius compensation |
G94 |
Radial cutting cycle |
G41 |
Tool nose radius compensation left of Contour (rear toolpost) |
G96 |
Constant surface speed control |
G42 |
Tool nose radius compensation right of Contour (rear toolpost) |
G97 |
Constant rotational speed control |
G50 |
Coordinate system setting |
G98 |
Feed per minute |
G65 |
Macro instruction |
G99 |
Feed per rev |
|
  PLC Elementary instructions |
Elementary instructions |
Functions |
Basic instructions |
Functions |
LD |
Read normally-open contact |
TMRB |
Timer |
LDI |
Read normally-closed contact |
CODB |
Binary conversion |
OUT |
Output coil |
ROTB |
Binary rotation control |
AND |
Normally-open contact in series |
MOVN |
Data copy |
ANI |
Normally-closed contact in series |
DECB |
Binary decoding |
OR |
Parallel normally-open contact |
JMPB |
Program jumping |
ORI |
Parallel normally-closed contact |
SP |
Subprogram |
ORB |
Parallel series circuit block |
SPE |
End of subprogram |
ANB |
Parallel circuit block in series |
ADDB |
Binary data adding |
 |
 |
SUBB |
Binary data subtracting |
Function instructions |
Functions |
ALT |
Alternative output |
END1 |
End of grade one program |
DIFU |
Up set |
END2 |
End of grade two program |
DIFD |
Down set |
SET |
Set |
MOVE |
And |
RST |
Reset |
PARI |
Parity check |
CMP |
Comparative set |
LBL |
Program jumping label |
CTRC |
Counter |
CALL |
Subprogram calling |
|
GSK980TD configuration software:GSKCC |
GSKCC runs in WINDOWS98/2000/XP, editing GSK980TD ladder, part programs, parameters, pitch error compensation data, tool compensation data, upload and download files and data between PC and GSK980TD. |
|
|
|